Grade Brief:
Virat Special Steels is the largest Supplier & Stockiest of H11 Hot Work Steel. H11 is an all inclusive hot work tool steel with hot rigidity and durability. Good thermal conductivity and invulnerability to hot cracking and can be water cooled to a constrained degree. Utilized for ejector pins, apparatus holders and shrink fit chucks.
According to the AISI classification system, tool steel H11 is a chromium-based steel alloy from the “H” family of steels. Due to its exceptional impact hardness, H11 is one of this group’s alloys that is employed the most frequently. Due to its exceptional resistance to cracking, including thermal fatigue cracking, gross cracking, and thermal shock during water cooling, H11 is also employed in hot tooling applications. Due to the balanced alloy composition, thorough hardening and air hardening of Tool Steel H11 cause very little deformation. A process called air quenching can also be used to harden H11.
Consult our Gurugram office for further assistance.
Meanwhile for more on Virat Special Steels;
Email Us: info@viratsteels.com.
Contact them by mobile numbers 98140 – 21775, 99991 – 24971 to 79.
Mode of Supply
Virat Special Steels is the largest stockiest and supplier of H11 tool steel in flat, square and round bar. We provide steel in all sizes as your requirements. H11 die steel is available in flat, square and round shape. Consult our team who will assist you for h11 steel query.
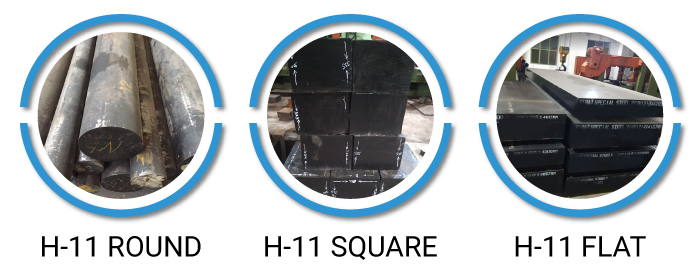
Steel Properties
Hot work tool steel with Chromium 5% has high strength and toughness, best thermal physical
phenomenon and in susceptibility to hot cracking. This provides the essential necessities for long tool
life in die-casting , Press Forging , extrusion processes etc.
Mechanical Properties:
Tensile strength | 1792 MPa |
Yield Strength | 1482 MPa |
Elongation | 8% |
Impact Toughness | 13.6-33.9 J/cm2 |
Hardness | 52-57 HRC |
Physical Properties
Coefficient of thermal expansionat °C | 20-100 | 20-200 | 20-300 | 20-400 | 20-500 | 20-600 | 20-700 |
10-6 m/(m*K) | 11.7 | 12.3 | 12.5 | 12.7 | 12.75 | 12.9 | 12.9 |
Thermal Conductivity °C | 20 | 350 | 700 |
W/(m*K)Annealed | 29.8 | 30.0 | 33.5 |
W/(m*K)Quenched & Tempered | 26.7 | 27.4 | 30.4 |
Machinability:
The machinability of H11 / DIN 2343 / AISI H11 is 75% to that of steels in the “W” group.
Heat Treatment & Processes:
Heat Treatment:
Steel Tool H11 / DIN 2343 / AISI H11. Annealing, hardening, air and oil quenching, and single- or double-tempering are the most common heat treatments, which are performed at temperatures of 840° F (450° C), 930° F (500° C), 1020° F (550° C), 1110° F (600° C), and 1200° F (650° C). Combining hardness, toughness, yield strength, ultimate strength, and ductility results in the best heat treatment, which also includes oil-quenching and double-tempering at 1020° F (550° C).
Hardening:
The austenitizing temperature, which should be between 1800° and 1850°F, the quenching medium, and the tempering parameters all have a role in how hard H11 / DIN 2343 / AISI H11 steel becomes. H11 / DIN 2343 / AISI H11 steel should be hardened by cooling in still air due to its extremely high hardenability.
Tempering:
Quenching H11 steel is tempered to make it more resilient and less brittle. Reheating the steel to a temperature that is lower than its critical temperature—typically between 500°C and 650°C or 932°F and 1202°F—and maintaining it there for a certain amount of time is the process of tempering. The ideal balance between hardness and toughness determines the precise tempering temperature and duration. These steels can also undergo double tempering once per hour at the chosen tempering temperature.
Forging:
Forging H11 / DIN 2343 / AISI H11 steel is normally done at a temperature between 1000 and 1200 degrees Celsius (1832 and 2192 degrees Fahrenheit). According to the required deformation properties and the manufacturer’s instructions, the precise temperature will vary.
Stress Relieving:
H11 / DIN 2343 / AISI H11 steel is heated to a particular temperature of 650 °C for two hours as part of the stress-relieving procedure, and it is then gradually cooled.
Normalizing:
H11 / DIN 2343 / AISI H11 Steel should not be normalised due to its air-hardening ability .
Annealing:
H11 / DIN 2343 / AISI H11 tool steels are annealed at 871°C (1600°F) and then slowly cooled at 4°C (40°F) in the furnace.
Nitriding:
H11 / DIN 2343 / AISI H11 steel can be nitride to give a hard surface at a temperature of 500 °C to 600 °C
Welding:
The surfaces of the dies attain temperatures of 700–800 °C during forging procedures. As a result, hardfacing these sections using nonferrous higher temperature hardfacing alloys like Stellite 6 can frequently increase the effectiveness and lifespan of the dies. The most crucial characteristics of Stellite 6 are its high hardness, galling resistance, hot corrosion and oxidation resistance, adhesive wear resistance, low friction coefficient, and lack of allotropic transformation up to 1100 oC. Due to its high alloy concentration and resulting hardenability, this steel is extremely susceptible to hydrogen induced cracking (HIC) and high cooling rates used during welding cycles. Due to this, the hardfacing characteristics of H11 tool steel with Stellite 6 in the TIG welding process have been examined in this study. The findings show that it is not possible to hardface this steel in its annealed hardfaced state; instead, preheating and intermediate temperatures between 310 and 370 oC are advised. Under these circumstances, 3mm was found to be the minimum thickness required to provide the hardness required (41-42 HRC) in the hardfacing layer.
Quenching:
After the soaking period, the H11 / DIN 2343 / AISI H11 steel is rapidly cooled by immersing it in a quenching medium. The choice of quenching medium depends on factors such as the steel’s composition and the desired hardness. Oil, water, and air are commonly used quenching media. Oil quenching provides a moderate cooling rate, water quenching provides a faster cooling rate, and air quenching provides the slowest cooling rate.
Soft annealing °C | Cooling | Hardness HB |
---|---|---|
750 – 800 | Furnace | max. 230 |
Stress-relief annealing °C | Cooling |
---|---|
approx. 600 – 650 | Furnace |
Hardening °C | Quenching | Hardness after quenching HRC |
---|---|---|
1000 – 1030 | Air ,oil or saltbath, 500 – 550 °C | 54 |
Tempering °C | 100 | 200 | 300 | 400 | 500 | 550 | 600 | 650 | 700 |
HRC | 52 | 52 | 52 | 52 | 54 | 53 | 48 | 37 | 31 |
Applications
Besides applications typical for the area of hot-work steels, this grade is especially used for ejector pins, tool holders, bridge kind tools, liner holders, extrusion tooling, Die Casting dies, Forging Dies, Hot work punches, Hot gripper dies, Aircraft landing gear and shrink work chucks.
Addition to other Grades:
HCHCR-D2 Steel , HCHCR-D3 Steel , P20+Ni Steel , P20 Steel , DB6 Steel , H13 Steel, H11 Steel, H21 Steel, H10 Steel, H12 Steel, M2 Steel, M35 Steel, M42 Steel, T1 Steel, DIN 2379 Steel, DIN 2080 Steel, DIN 2738 Steel, DIN 2311 Steel, DIN 2714 Steel, DIN 2344 Steel , DIN 2343 Steel, DIN 2581 Steel, DIN 2365 Steel, DIN 2606 Steel, DIN 3343 Steel, DIN 3243 Steel, DIN 3247 Steel, DIN 3355 Steel AISI D2 Steel, AISI D3 Steel, AISI P20+Ni Steel, AISI P20 Steel, AISI L6 Steel , AISI H13 Steel, AISI H11 Steel, AISI H21 Steel, AISI H10 Steel, AISI H12 Steel, AISI M2 Steel, AISI M35 Steel, AISI M42 Steel , AISI T1 Steel
Our Global Presence:
India, Nepal, Dubai, Thailand, Vietnam, Saudi Arabia, United Arab Emirates , Qatar, Kuwait, Iran, Turkey, Portugal, Spain, Poland, UK, USA, Canada, Brazil, Mexico, Belarus, Australia, New Zealand and many more..
We Provide our Special Steels in All Major Cities India.
Agra, Alwar,Ambala, Anand, Bhiwadi, Dehradun, Ghaziabad, Haridwar, Rudrapur, Delhi, Faridabad, Kanpur, Noida, Gurgaon, Manesar, Kundali , Chandigarh, Waluj , Vadodara, Pimpri – Chinchwad, Rajkot, Jaipur, Ahmedabad, Pithampur, Surat, Amravati, Vadodara, Indore, Bhopal, Ranchi, Jamshedpur, Howrah, Kolkata, Pune, Thane, Nashik, Mumbai, Navi Mumbai, Nagpur, Ambattur, Bangalore, Belgaum, Chittoor, Dindigul, Hyderabad, Ernakulam, Chennai, Secunderabad, Visakhapatnam, Coimbatore, Mysore, Nellore, Kochi, Thiruvananthapuram, Trivandrum, Vijayawada, Guntur, Tirupati, Nazarathpet, Kakinada, Kurnool and many more..