In the world of industrial tooling, H13 tool steel stands out as a versatile and high-performance material, essential for applications requiring exceptional hardness, toughness, and resistance to thermal fatigue. At Virat Special Steels, we specialize in providing quality H13 steel and expert support to meet diverse industry needs, whether for die casting, molding, or forging applications. This blog explores the key properties, applications, and machinability of H13 tool steel, which make it a go-to solution for tooling requirements worldwide.
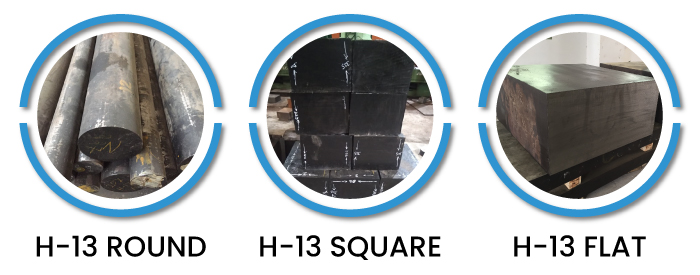
Understanding H13 Tool Steel
H13 tool steel is a chromium-molybdenum-vanadium alloy, specifically engineered for high-stress applications, particularly in environments with elevated temperatures. Known for its unique balance of hardness, toughness, and heat resistance, H13 is widely used in die casting and hot forging tools where it faces constant wear and thermal cycling. Here are some of the notable properties of H13 steel that make it so valuable:
- Hot Work Capability: H13 is classified as hot work tool steel, designed to withstand high temperatures and repetitive heating and cooling cycles.
- Excellent Hardness: H13 tool steel hardness is in the range of 44-54 HRC, depending on heat treatment, which allows it to resist deformation under high-stress conditions.
- Good Toughness: H13 offers a high level of impact resistance, which is essential for tools that encounter high-pressure and high-speed operations.
- Enhanced Thermal Fatigue Resistance: The steel’s composition and structure allow it to withstand thermal cycling without cracking, which is ideal for die casting and extrusion dies.
Key Properties of H13 Tool Steel
The H13 tool steel material properties combine to deliver exceptional performance in high-stress, high-temperature conditions:
- Chemical Composition: H13 is composed of chromium, molybdenum, and vanadium, which contribute to its high strength and resistance to heat and wear.
- Mechanical Properties: The mechanical properties of H13 steel include a tensile strength range of 1000–1300 MPa and yield strength around 900 MPa, ensuring robustness under stress.
- Hardness: In its raw state, H13 raw material hardness ranges from 18 to 22 HRC, but with proper heat treatment, it can reach 44-54 HRC, enhancing wear resistance significantly.
- Thermal Conductivity: The alloy’s moderate thermal conductivity aids in rapid cooling, which is essential in die-casting applications to reduce cycle times and improve efficiency.
- Machinability: Despite its hardness, machining H13 tool steel is feasible with the right tooling and techniques. It can be effectively machined in the annealed condition, although machining becomes more challenging as hardness increases.
Applications of H13 Tool Steel
Due to its ability to endure high temperatures and maintain structural integrity under stress, H13 steel is widely used across various industrial sectors. Some of its primary applications include:
- Die Casting Dies: Its resistance to thermal fatigue and wear makes H13 ideal for molds used in die casting, where repeated exposure to molten metals demands a material that won’t degrade under high heat.
- Forging Dies: H13’s toughness and hardness are suited for hot forging, where tools must withstand high impact and compressive forces.
- Extrusion Tools: H13 is frequently used for tools involved in the extrusion of metals due to its durability and ability to withstand high-pressure environments.
- Plastic Molding Dies: In plastic molding, H13 is used for molds that need to withstand both high temperatures and pressures while producing intricate shapes.
Machining H13 Tool Steel: Tips and Techniques
Machining H13 tool steel requires specific considerations due to its hardness and toughness. Here are some strategies that can help optimize machining processes with H13:
- Use of Carbide Tools: Given its hardness, H13 should ideally be machined with high-quality carbide cutting tools to ensure precision and reduce tool wear.
- Moderate Speeds and Feeds: For effective machining, it’s recommended to use moderate cutting speeds and feeds to prevent overheating and maintain tool integrity.
- Coolant Utilization: Applying a coolant during machining helps reduce heat build-up, especially in high-speed operations, which can protect both the tool and workpiece.
- Heat Treatment: To improve machinability, H13 is typically machined in its annealed state and then heat-treated to achieve the desired hardness for its end application.
Why Choose Virat Special Steels for H13 Tool Steel?
At Virat Special Steels, we are committed to providing top-quality H13 tool steel tailored to meet the demands of your applications. Our expertise in steel distribution, coupled with our focus on high standards and customer support, ensures that you receive only the best material, whether you need H13 die steel, mold steel, or hot work tool steel.
Our team of experts is here to help guide you through selecting the right material for your needs, offering insights on H13 material properties, mechanical properties, and recommendations for machining and heat treatment.
Conclusion
Whether you are in die casting, hot forging, or extrusion, H13 tool steel provides the reliability and durability essential for long-lasting, high-performance tools. At Virat Special Steels, we stand ready to supply you with premium H13 steel that meets the highest quality standards. Contact us today to learn more about how H13 tool steel can serve your production needs and help your business achieve optimal efficiency and precision.
Partner with Virat Special Steels for quality, expertise, and reliable H13 solutions.
Mode of Supply: Virat Special Steels is the largest Supplier & Stockiest of H13 Steel in India. Consult our team who will assist you for H-13/ DIN 2344 / AISI H13 steel query. https://www.viratsteels.com/h13.html
Size Range in Forged / Rolled Bars:
Rounds: 13mm Dia to 1500mm Dia
Rectangular: Thickness 13mm – 500mm / Width 13mm to 1500mm